Continued from page 1
The Plummeting Price Drops of 3D Printing
When 3D printing got its start only defense industry companies and the Boeings of the world could afford them. They went from a quarter of a million dollar machines, then to 50k machines, then they broke through the 10k barrier. But it was companies like MakerBot that caused the big shift to happen.
Boston is a pretty good place for this because, one, there are other 3D printing companies here, but probably more importantly, the CAD companies are here. They are all here; they are all five or ten minutes from where we are.
“When MakerBot showed up with a two or three thousand dollar printer that marked a big shift,” says Kawola. But Stratasys acquired MakerBot when the latter company was going through their major “Hype-cycle” moment. “Stratasys was the company with the core patent about extruding plastic through a nozzle,” says Kawola. “Now MakerBot, Ultimaker and a whole bunch of other guys are using technology that Stratasys invented.”
With the 3.0 era, companies like Ultimaker are offering the market easy-to-use 3D printers for under three thousand dollars. This dramatically opens up the market, including the AEC industry which Kawola says is about 5 percent of their total business.
“Education is the strongest market after manufacturing for 3D printers,” adds Kawola. But the AEC industry includes manufacturers of building products—a touch point where the “design-to-fabrication” intersection becomes a highly interesting possible point of disruption within AEC as a whole.
Ultimaker’s Positioning
The Dutch company got started with three guys trying to do a low-cost 3D printer for the maker crowd. In 2011, they started selling 3D printer kits that you could buy over the Internet with a credit card. “Makers were attracted to Ultimaker because they could tinker with it—due to its open-source nature,” said Kawola.
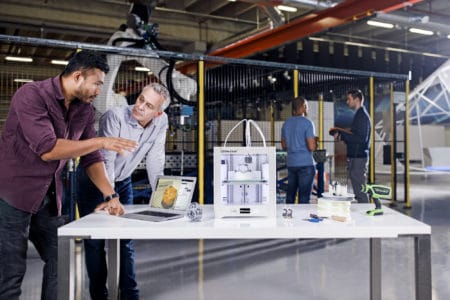
02 – Ultimaker 3D printers are found on the carpet floors of design and engineering offices as well as in labs and factory settings. (image: Ultimaker / Architosh. All rights reserved.)
The manufacturing crowd, however, was focused on the larger existing players. “There was a bias in the enterprise market against companies like Ultimaker,” he adds. Now things are slowly changing and Ultimaker’s potential market audience is evolving. “Because they are only $5K, they are now at a disruptive price point,” Kawola says, “and now they are looking at this and thinking we should maybe get one—or five.”
This dynamic change means that Ultimaker is no longer just a fan favorite for the makers, much bigger companies are looking at their 3D printers for their engineering and design workgroups. “Our market is where the engineers are,” says Kawola. China’s a big market, Japan’s a big market, South Korea’s a big market. When we think about distribution in the world—and we track where all the engineers are—generally the market breakdown is about 40 percent Europe, 40 percent North America and 20 percent Asia-Pacific.”
Because they are only $5K, they are now at a disruptive price point, and now they are looking at this and thinking we should maybe get one—or five.
“We were underrepresented here in the US, but Ultimaker is growing fastest here in North America,” he adds. Kawola is modest about this growth in the US, noting that the rivals make good technology also. “We like to say our products are more robust and we deliver a very good product and we have materials and parts all over the world,” he adds, “increasingly we are global.”
Ultimaker has two factories at the moment. One factory is in the Netherlands and the other is in the US in Memphis. He explained that there is a lot of contract manufacturing in Memphis as well as fulfillment centers.
Talking About the AEC Market Challenges
Part of the reason why this interview came about had to do with Ultimaker’s appearance at the 2018 AIA National Convention. Are architects interested in 3D printers? Absolutely, many are, as evidenced by the high traffic at the Ultimaker booth. (see image 03 below) But there are still interesting challenges in front of wide-spread adoption to 3D printers in architecture offices.
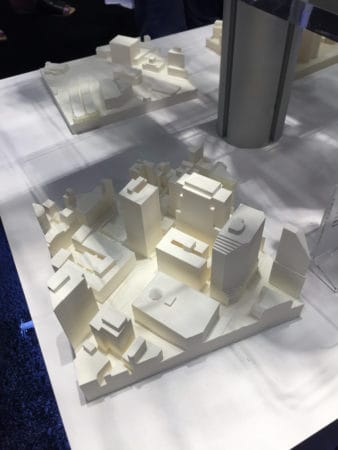
03 – Architecture and urban models on display at the Ultimaker booth at the AIA National Convention and Exhibition in 2018. (image: Architosh. All rights reserved.)
Kawola notes that selling to architecture firms is just 5 percent of their mix. I asked him what are the challenges getting in the way of larger adoption in architecture firms. “I’ve been selling 3D printers to architects for 20 years,” he says, “but part of the challenge is the difference between buildings and parts in manufacturing. In manufacturing, the part is a solid model, it is the real thing, in scale. When you are using 3D software in architecture it is still a “rendering” and it may not be solid, and the walls might not touch, or the features are so small that when you scale it down there are obstacles there.”
Kawola noted that in the architectural industry there has always been a challenge with the data. “There is more of a skill-level in architecture to go from design to printed part today.” In the manufacturing world, the 3D printers can print those parts at 1:1 scale, but such machines must print buildings or segments of them at vastly different scales. Still, he says that they continue to see widespread adoption of their Ultimaker 3D printers by architecture firms.
More and more architecture firms are delving into “digital design to fabrication” workflows, whether in research labs or as tried and true one-off production runs. The way in which 3D printers work says a lot about what is possible for various industries as well.
Why Buy a 3D Printer—Benefits and Opportunities in Industries
One of the major trends in manufacturing is weight reduction, which also applies to the world of buildings—products and parts that are transported often great distances for erection in a building on site. I asked Kawola where he saw 3D printing playing a role in this weight-reduction movement.
“I think that is a huge opportunity that is only now just being realized a little bit.” He noted that in the history of 3D printing nearly all the value has been in simply making parts at scale for iterative design workflows and validation. But he says that today one of the side advantages of 3D printing is that your geometry constraints sort of go away. “Molding parts, casting parts, machine parts, you always have constraints,” he adds, “but with 3D printing, those constraints largely go away.”
Molding parts, casting parts, machine parts, you always have constraints, but with 3D printing, those constraints largely go away.
Kawola says that generative design software has changed the way people design with CAD. “If you use that organic generative design software to create something,” he adds, “now the challenge is ‘can you actually make it.?’ So 3D printing is practically the only way you can make it; so I think those ideas are coming together, and I think the industry that is probably the most forward on that is aerospace.”
He says that in aerospace if you tell someone you can make something five percent lighter there is no incentive not to pursue it, they know that five percent less weight comes with a huge benefit down the line. “The aerospace industry is the most out there in pushing this weight reduction and in some ways is pushing the industry in the development of metal 3D printing,” he adds.
Weight reduction and 3D printing have different economics for every industry. The car industry might find a way to make a part several grams lighter, but if the cost of that part rises 30 percent in doing so, it doesn’t matter if the car may become more fuel efficient, the car company isn’t likely going to do it. But the aerospace industry and other industries where weight optimization is critical to costs are likely going to pursue such endeavors no matter what the cost.
next page: Ultimaker’s 3D Printers and How They Work
Reader Comments
Comments for this story are closed