Continued from page 2
Part 3: Introduction to Architectural Exploration with Inspire 2014
For some readers this section is the entire part of the feature you have been waiting for. Developing more complex architectural studies with Inspire 2014 takes investment in learning the nuances of the program. While the examples shown in solidThinking’s literature are quite amazing, getting to such results yourself requires understanding the program’s limitations and subtleties.
Advertisement
We have an entire dedicated in-depth companion feature devoted to this subject where we show some amazing things others are doing as well as work through several case studies demonstrating the use of the program in architectural workflows.
Bus Station Roof Study
In our first efforts we looked at creating a roof structure for a bus station, or some such structure. Supports are from the center while a larger roof cantilevers both sides. A “design space” (shown in reddish brown) is given an approximate shape. Next, a continuous block for support is set under the entire middle support section. One could think of this as the foundation. (see image 10)
The next element is the roof which is shown simply as a loaded, rectangular mass. After placing supports at the bottom element, placing loads on the roof element, and defining the shape controls (red planes) a mass optimization run is begun. The result is generated within 10 minutes. Importantly, we should review the optimization palette and share some tips.
The optimization palette includes some important settings and two fundamental objectives. You can either optimize around maximum stiffness or around minimal mass. The image below shows the maximum stiffness option with mass targets indicated at 30 percent of the design space volume. (see image 11)
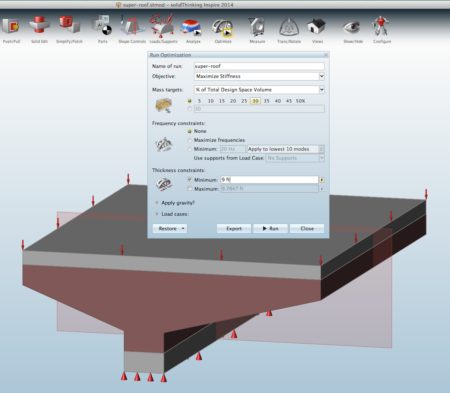
11 – The optimization palette continues two fundamental options, designing for maximum stiffness or minimum mass.
A key discovery during the review process was that the minimum thickness constraint value was often too little. As a result Inspire 2014 would often take far too long to calculate the results or not complete them at all. The tip came from the folks at solidThinking that Inspire considers every model element—not just the “design space” in its minimum thickness constraint. It was therefore suggested to raise the default values that appear in the input field, making sure that no model element, outside the design space, has a thickness smaller than the “minimum thickness” across its key dimensions. This dramatically improved optimization run times, and greatly sped up the review process itself.
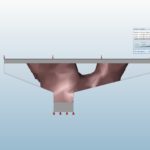
13 – The side view shows that when we thin the load block above the design space the optimization pushes mass further out to the edges of the design space, due to the decreased self-support in the load block itself.
Above you can see a series of images showing the mass created by the optimization. Note that the entire structure consist of mass elements (blocks) of solid steel. Inspire allows the user to choose other material options, such as aluminum, titanium, plastic and so forth. The top grey element has the load applied to it. Given its initial thickness, the extent to which the organic shaped structural mass that needed to reach out to support its edges was minimal. When we reduced the thickness of the roof load block, the optimized mass changed and reached out further to the roof’s edges. (images 11 – 12). Again, think of the shapes being shown and note that, like in the beam problem above, the top load block begins to participate in the resultant structural forms like a top flange.
Unlike the beam problem however, the load block can only be so thin before it itself causes massive displacement due to the forces. This is why Inspire has its name. The resultant shapes are meant to inspire the creative process, not dictate structure and structural arrangement. The roof on the bus shelter structure above might wish to be light trusses itself running perpendicular to the view or a heavy metal and concrete composite deck that can span web-like truss structures in steel that reflect the shape of the minimized mass.
In the video below you can see the deflection and displacement of the resultant “optimized mass” and this video is very informative for any designer and engineer.
The video above shows the displacement and tension versus compression on the optimized mass for the bus station roof structure.
As you can see from the images below the asymmetry of the design causes unequal displacement. The user can explore multiple runs with increases and decreases of the roof load block and thicker optimized mass for the design space.
Another view below shows the semi-transparent function available in Inspire, which looks a lot like x-rays, which you will see more of in the companion architectural feature on Inspire 2014. (see image 14)
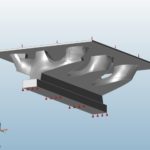
15 – Inspire 2014 now features a smoothing function that smooths out the organic, generated optimized mass model.
One of the key goals with using Inspire 2014 for architecture is to find interesting structural forms. Some readers may be wondering about the use of concrete as a structural material. Can you use it? The short answer is no. Certain types of materials, like wood and concrete, don’t offer the right physical properties that lend themselves to the solvers in Inspire 2014. We will discuss this in more detail in the companion feature.
Looking at the Possible
In this brief look at a bus shelter roof type of problem we were able to generate an interesting set of forms and options. The next logical step after this type of work is to then take the smoothed model out (export out) to another CAD modeling tool and create more refined geometry that responds to the lessons inherent in the optimized massing model.
At that point the work down in Inspire may end for architectural objectives. While, in product and parts design, another iteration may likely take place. The analysis tool works fully on final resolved design forms, checking for all the same stresses that are run on “optimized mass” parts. This iterative process can be quite detailed but Inspire 2014 has the ability in such analysis to assign various constraints like displacement, frequency, and stress. If you notice at the beam problem (image 08), a displacement constraint was exceeded during the run. This informs the designer that the design goals are not working and to revise the work.
We have a lot of interesting work to show you that was done in the areas of architectural form exploration, using Inspire 2014. In the first image below we show some teaser work on an bridge, platform or dock structure whose supports were far below the level of the even load it carried. Think bridge design, for example. (see image 16)
In the next example a simple un-equal roof shape is caring unequal loads, resulting in an asymmetrical optimized mass. Again, like the basic beam problem, the loads are applied to a load block which, being made of steel, in the end must be read as part of the structure. In this case, the top chords of a truss form. (see image 17)
In the final image below, a fully developed architectural concept that has been taken through advanced iterations in Inspire 2014 shows an organic form holding up a futuristic linear structure high above the ground. (see image 18)
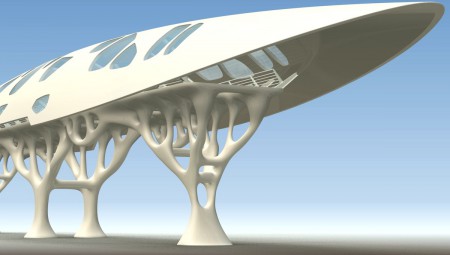
18 – An fully developed architectural concept. (image: courtesy of solidThinking Inc. All rights reserved.)
This is an example of what can be generated with a combination of the Inspire and Evolve solidThinking software toolkits, with or without combinatory efforts in other CAD tools.
Conclusions and Recommendations
solidThinking Inspire is a truly unique tool and in a class by itself. The program acts as a hub for computer-aided engineering (CAE) type analysis brought to the front-end of the design process. In the architecture space, the innovation in Inspire aligns well with the trend in what some call “front-ending” the analysis. Given the rising importance of our environment in the face of global emissions and the push for more sustainable buildings, key innovations in architectural software have primarily focused on testing the energy consumption of structures earlier in the design phase—i.e.: bring analysis to the front end of the design process where bigger impacts can be made.
Advertisement
Inspire 2014 helps designers make parts, products and assemblies better by addressing the strength versus weight ratio. For architectural work, the company has expressed the product’s value a bit differently, focusing on finding innovative (and yes! lighter weight too) structural forms. To be perfectly honest, Inspire 2014’s help and literature is mostly aimed at product and industrial designers, not architects.
To make this very good product even better there are some low-hanging fruit to address. An on-boarding process for the architectural professional in terms of what does it mean to focus on workflows that eliminate weight in building mass? What types of problems at what scales can be addressed? How do they get setup in the software? This would be a good start.
Functionally, Inspire doesn’t allow you to open multiple model windows at the same time. So you can’t be working on two problems at once in discreet windows. It would be nice too if there was a way to distribute runs (optimization and analysis calculations) across multiple computers, a la, render farm style. Anything to speed up design iteration. And speaking of iteration, a side-by-side ability so a designer can compare two closely developed solutions might also be useful.
In the final analysis, any product or industrial designer seriously interested in minimizing weight while retaining strength objectives will find real job and useful results in Inspire 2014. The tool is also simply fun to explore and play with, making the design process quite engaging. That’s one of the reasons why architects in particular might find using it deeply rewarding over time—it sponsors curiosity in the user in a way that engages design thinking. —- ANTHONY FRAUSTO-ROBLEDO, AIA, LEED AP, Editor
Pros: Despite the sophistication behind the technology, the user-interface is remarkably intuitive and easy to engage; excellent new solver technology helps designers explore deeper analysis; good improvements to modeling features in refined push/pull tools, new sketch plane features and new parts from solids are all excellent—the program is a pleasure to model quickly in; reliable Boolean tools and good new improvements in tool groupings in the toolbar; new smoothing feature and ability to explore out to other CAD tools; superb tutorial and help tools with text and video.
Cons: there needs to be more information to provided to help those in architecture work with the software; it’s not possible to work on two problems at once in discreet workspaces despite runs that work in the background; the program reports in OS X Force Quit dialog as being “non-responsive” in the early stages of some optimizations, when in fact the program is not hung.
Advise: A truly engaging tool that most product and industrial designers would benefit from having in their arsenal. Various classes of architects may find a healthy range of objectives to be solved by Inspire. The technology has great promise for the architecture and architectural engineering industry by bringing more analysis work to the front end of the design process.
Cost: Inspire 2014 starts at 5,995.euro or 7,995.USD.
Reader Comments
Mike Laney liked this on Facebook.
Matthew Ivanov liked this on Facebook.
Mike Laney liked this on Facebook.
Matthew Ivanov liked this on Facebook.
In this product review, Architosh looks at the unique solidThinking Inspire 2014 CAE-based industrial design and arc…https://t.co/5hoRdBJ7F0
In this product review, Architosh looks at the unique solidThinking Inspire 2014 CAE-based industrial design and arc…https://t.co/5hoRdBJ7F0
http://t.co/GFQFQ7SMgi — can solidThinking Inspire 2014 add innovation to architectural professionals? Read on! http://t.co/OXUG0ddBhF
http://t.co/GFQFQ7SMgi — can solidThinking Inspire 2014 add innovation to architectural professionals? Read on! http://t.co/OXUG0ddBhF
@solidThinking Inspire 2014 http://t.co/o9yTXhmUWh by Anthony Frausto-Robledo #mcad #cad
@solidThinking Inspire 2014 http://t.co/o9yTXhmUWh by Anthony Frausto-Robledo #mcad #cad
Check out @architosh review of Inspire for the Architectural market. http://t.co/USw0KTZC7v #architecture, #design, #software
Check out @architosh review of Inspire for the Architectural market. http://t.co/USw0KTZC7v #architecture, #design, #software
Comments are closed.